在钣金成形仿真中,摩擦是影响材料流动、成形极限、起皱与破裂等关键行为的核心因素之一。而在AutoForm中,如何合理设置摩擦系数,尤其是在不同区域、不同接触面上进行分层设置,并结合真实工况进行位置相关摩擦模型调试,直接决定仿真的物理真实性与工程指导性。很多工程师在项目过程中会遇到的问题,不是“有没有设置摩擦”,而是“摩擦设置是否合理”“摩擦变化是否贴合实际”。本文将围绕“AutoForm摩擦系数如何分层设置”与“AutoForm位置相关摩擦模型调试”两个维度,提供可实操、可验证的详细思路,帮助用户构建更贴合实际的高精度摩擦模型。
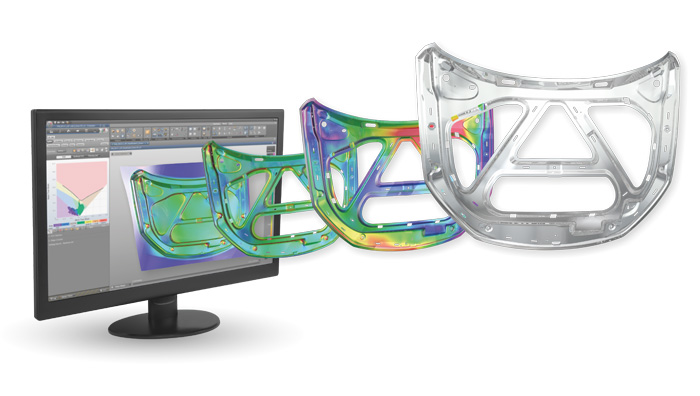
一、AutoForm摩擦系数如何分层设置
摩擦系数μ不是一个静态值,它在实际冲压过程中因润滑条件、接触区域、材料属性等因素而异。在AutoForm中,可以通过多种方式对摩擦进行“分层”、“分区”或“分界面”设定,使模拟尽可能反映真实工艺环境。
1.AutoForm中摩擦模型的基本概念
在AutoForm软件中,摩擦模型主要分为以下几类:
恒定摩擦模型(ConstantFriction)
设定一个固定μ值,适合初期快速仿真,精度有限。
接触相关摩擦模型(ContactDependent)
根据接触对(如模具-板料)分别设置不同摩擦值。
位置相关摩擦模型(PositionDependent)
根据板料上不同区域,赋予不同摩擦系数(比如中间润滑较好,边缘润滑较差)。
压力相关摩擦模型(PressureDependent)
μ值会随接触压力的大小变化,模拟压边时的润滑效应衰减。
其中,后两者(位置相关与压力相关)是实现“分层摩擦设置”的关键。
2.实现摩擦分层的主要方法
方法一:通过工具-板料接触对(Tool-BlankPair)设置不同μ值
适用于上下模具与板料之间摩擦不同场景:
打开ContactSettings;
添加多个ContactPair(如:Die-Blank,Punch-Blank);
分别设定摩擦值,例如模具上模区域μ=0.12,下模区域μ=0.08。
这种方式适合较粗粒度的摩擦控制。
方法二:在板料上定义“摩擦区域”实现空间分层
进入PartDefinition→AssignFrictionMap;
使用GeometryMap工具手动绘制区域(如边缘、中心区域);
为每个区域分别指定摩擦值;
系统会自动将这些分区映射到仿真板料网格中。
这也是“位置相关摩擦模型”的基础,尤其适合分析中间润滑vs边缘干摩的效果差异。
方法三:采用MaterialCard内的摩擦层设置
如果使用高级材料模型,可以在材料卡中为不同层次(如表面层、氧化层)设定摩擦;
选择材料卡→FrictionSection;
激活LayeredFriction设置,分别设定TopLayerμ、BaseLayerμ;
在多层板仿真中非常实用。
方法四:通过FrictionLaw设定非线性摩擦响应
摩擦值可以依据单位压力、相对滑移速度变化;
进入Friction→CreateFrictionLaw→定义函数μ=f(p,v);
实现动态摩擦调整,更贴近工业环境中润滑油膜厚度被压破的效应。
3.分层设置中的注意事项
每个区域网格精度要足够,否则摩擦值分布会变得不连续;
模型中存在多个摩擦源时(模具、拉延筋等),需统一设定逻辑;
仿真报告中可启用摩擦分布图查看每个区域的实际μ值是否被正确应用。
二、AutoForm位置相关摩擦模型调试
完成摩擦分层设置后,还需对模型进行调试与验证,确保仿真结果能正确反映实际工况。这一环节不可忽略,尤其是在多段工艺、多种润滑剂、复杂模具接触的场景下更显重要。
1.常见问题与异常现象
现象一:板料边缘起皱但中心无明显变形
原因:边缘区域摩擦设置偏低或偏高,导致材料无法有效约束;
解决:适当提高边缘区域μ值,或加大压边力以增加法向压强。
现象二:材料过早破裂或回弹异常
原因:中部摩擦过大,材料流动不顺畅,应力集中;
解决:降低中心区μ值,并检查润滑模型是否设置为恒定值。
现象三:成形极限线预测偏差大
原因:摩擦模型不含压力依赖性,未反映压强-摩擦关系;
解决:改用μ=f(p)型摩擦函数或引入表面粗糙度影响因子。
2.调试流程建议
①启用摩擦分布可视化图层
在仿真结果视图中,开启FrictionDistribution图;
快速定位高μ值区域、高滑移速度区域,判断是否与预期一致。
②进行单变量调试
固定所有参数,仅变动摩擦模型;
观察厚度减薄图、成形极限、应力分布的变化,评估敏感性。
③对照实物试模或划痕试验结果
若有条件,建议对实模件表面进行油膜划痕观测;
比较仿真摩擦线方向与实际划痕一致性,作为调试依据。
④与材料试验部门协作调取真实摩擦因子
多数钢厂、铝厂会提供在不同润滑条件下的摩擦系数参考值;
将这些经验值作为基础输入进行校准更具可靠性。
3.高级调试建议:构建摩擦响应数据库
为常用板材与润滑剂建立μ-压力-速度映射表;
将经验模型或试验模型封装为“FrictionTemplate”供跨项目调用;
通过批量仿真工具(Batch)测试不同摩擦组合对成形质量的影响范围;
最终在工艺窗口图中将摩擦变化因素纳入优化变量体系。

三、摩擦模型在成形仿真中的未来趋势与建议
1.向多物理耦合摩擦模型演进
未来版本可能支持板料表面温度与润滑膜厚的协同演算;
模拟不同冲压速度或热成形时,μ随温度动态调整。
2.摩擦模型与AI辅助优化结合
AutoForm可通过DOE参数优化功能,将摩擦值纳入敏感性分析;
与实际试模反馈形成闭环,训练优化模型,实现快速收敛。
3.与模具表面处理数据整合
表面涂层、喷砂处理的粗糙度可作为输入因子,影响μ函数;
建议在模具设计阶段记录摩擦相关参数,供仿真直接调用。
总结
AutoForm摩擦系数如何分层设置与AutoForm位置相关摩擦模型调试已成为现代冲压仿真不可或缺的两项核心能力。通过从“空间区域”、“接触界面”、“物理条件”三个维度灵活控制摩擦值,并配合可视化分析与实验数据调优,能大幅提升仿真预测精度,缩短试模周期,增强数字样机的决策指导力。未来建议在企业级工程流程中将摩擦参数标准化管理,构建经验数据数据库,推动从仿真建模走向过程智能预测的新阶段。